Servicing up to 150 buses required a specialist knowledge of equipment, design and workspace efficiency, so Kangaroo Bus Lines called Levanta to help with their fit out. Devising the perfect strategy to combine large scale efficiency, safety and productivity, the result was a resounding success.
Project Challenge
To work closely with a building and construction company to design, manufacture, supply and install a total workshop facility for the Kangaroo Bus Lines Depot at Burpengary that can service and maintain up to 150 buses. This was a green field site which required significant input and expertise to deliver a highly flexible and workable solution to the client.
Our Solution
Designed from the concept stage in conjunction with the client and the builder, this project combined the full scope of our workshop solutions, incorporating engineering, manufacturing, sourcing, supply and installation.
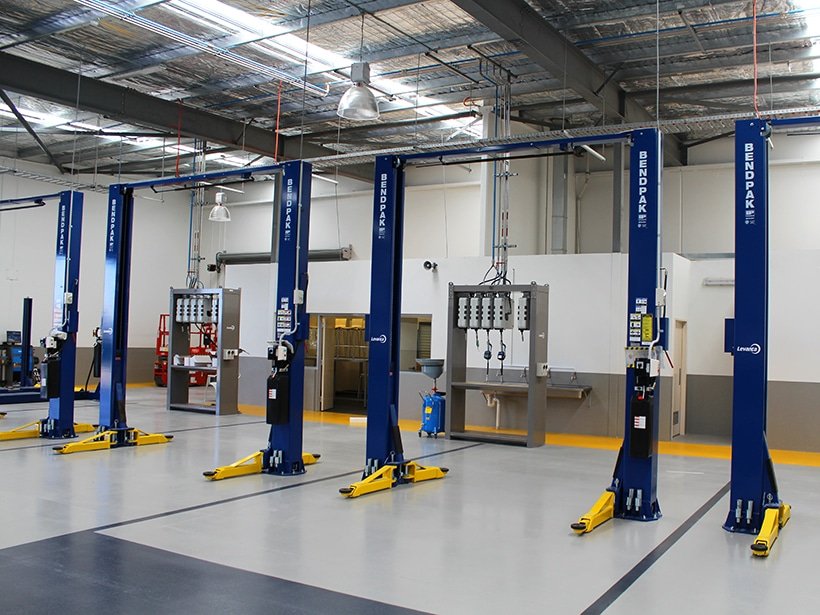
The project included:
- The design and install of a heavy duty suspended ceiling pit, with all steel work being hot dip galvanised
- Incorporating heavy duty air operated rolling work platforms, air/hydraulic rolling pit jacks and an exhaust extraction system that worked in conjunction with the pit lighting
- Full oil delivery system that pumps 3 grades of oil, grease and coolant to hose reel gantries
- Bulk new oil, new coolant, waste oil and waste coolant tanks
- BM Roller Brake Tester and Shakers
- 2 x Manual wash bays with high pressure hose and hose reels
- Heavy Duty Computerised Wheel Balancer
- Parts Hot Wash
- Set of 6 Liftmax 6.5t wired mobile column lifts
- Rolling Oil Drainers and waste oil & coolant pumps and reticulation
- A range of small workshop equipment including Wheel Trolley and Jacks
Client Benefit
Kangaroo Bus Lines have received a top of the line facility that focuses on the safety of their staff and the buses that service Brisbane. This state of the art facility services and maintains up to 150 buses with ease. Allowing for multiple service, cleaning and repair bays, tradesman can work simultaneously to keep up with the heavy demands of this critical public service.
Get in touch with us today
Our expert team will be happy to answer any question you have, or provide you with an estimate
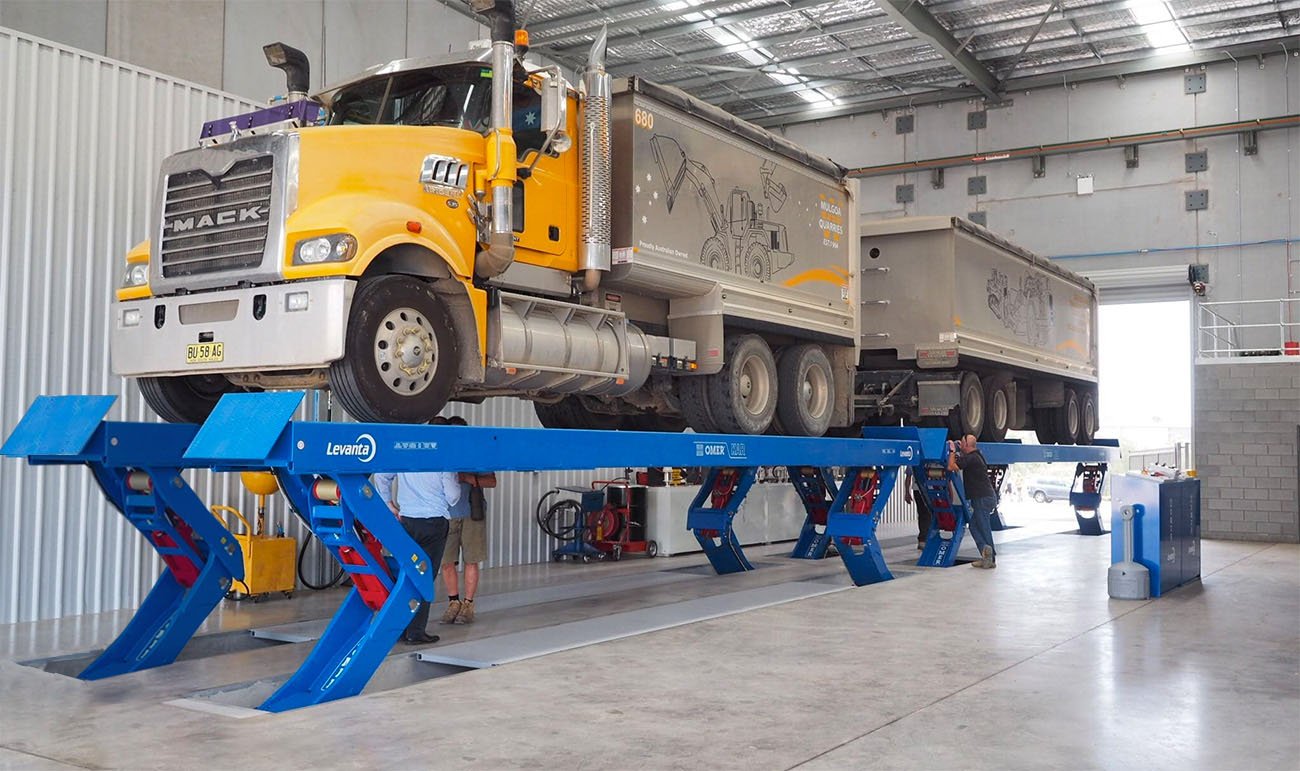